Chemical Reactors – Pharmaceutical Reactors, API Plant Reactors, Reactors For Chemical Plant, Liquid Reactorsbr Manufacturers & Exporters
Offering a high quality Jacketed Vessel in different capacities ranging from 50 liters to 15,000 liters. Fabricated from superior grade of stainless steel, these vessels can be provided with different types of agitators such as anchor type, propeller type, paddle type, pitched blade turbine type of high-speed homogenizer. The unique design of our reaction vessels allow the conditions to be controlled for fastest possible chemical reaction.
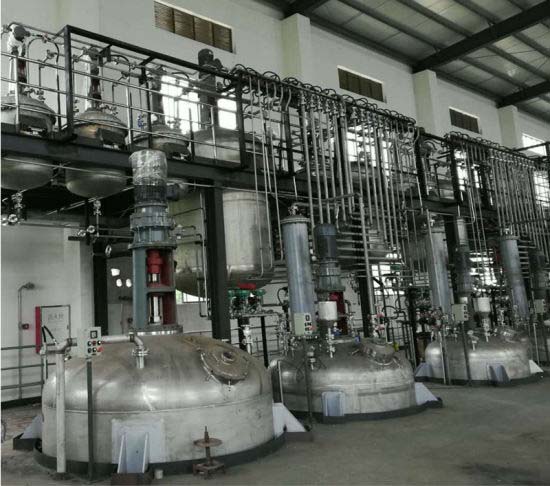
APPLICATION:
Abster™ Equipment makes Premium quality of chemical reactor is a covered volume in which a chemical reaction takes position. It is usually understood to be a process vessel used to carry out a chemical reaction, which is one of the classic unit operations in chemical process study. Customized Design of a chemical reactor contract with manifold aspect of chemical manufacturing. Chemical engineers intend reactors to make the most of net present charge for the given response. Advanced Technology of chemical reactor make certain that the reaction proceed with the maximum effectiveness in the direction of the required output product, produce the highest give way of product while requiring the smallest amount of money to purchase and function. Standard functioning expenses include raw material costs, energy removal, labour, energy input, etc. Energy changes can come in the form of heating or cooling, frictional pressure loss, agitation, pumping to increase pressure.
OVERVIEW OF CHEMICAL REACTOR:
Complete range of chemical reactor is mainly universal essential types of pipes or tubes (for laminar flow reactors and plug flow reactors) and chemical reactors are tanks (anywhere the reactants mix in the entire volume) Both types can be used as incessant reactors or batch reactors, and either may contain one or more solids (inert materials, catalysts or reagents), but the reagents and products are characteristically fluids (liquids or gases). Reactors in incessant process are classically run at steady-state, while reactors in batch process are of necessity function in a fleeting state. When a reactor is bring into process, moreover for the first time or after a shutdown, it is in a fleeting state, and key procedure variables change with time.
There are three idealised replica used to approximation the most significant process variables of dissimilar chemical reactors:
- Batch reactor model,
- Continuous stirred-tank reactor model (CSTR), and
- Plug flow reactor model (PFR).
Batch reactor
The simplest type of reactor is a batch reactor. Wide Range Of materials are laden into the reaction proceeds with time batch reactor and a batch reactor does not reach a stable state, and pressure, volume, and control of temperature is frequently essential. Many batch reactors consequently have ports for sensors and material input and output. Batch reactors are characteristically used in small-scale manufacture with reaction and biological materials, such as in pulping, brewing, etc single instance of a batch reactor is a pressure reactor.
CSTR (continuous stirred-tank reactor):
In a CSTR, one or more liquid reagents are establish into a tank reactor which is classically stirred with an impeller to make sure appropriate mixing of the reagents at the same time as the reactor effluent is separate. In-between the volume of the tank by the standard volumetric flow rate from side to side the tank gives the space time, or the time necessary to development one reactor volume of fluid.
PFR (plug flow reactor):
In a PFR, from time to time called continuous tubular reactor (CTR) one or more fluid reagents are pumped from side to side a pipe or tube. The chemical reaction proceeds as the reagents travel from side to side the PFR. In this kind of reactor, the varying reaction rate create a gradient with admiration to detachment traverse; at the inlet to the PFR the rate is extremely high, but as the concentrations of the reagents diminish and the attention of the invention increases the reaction rate slows.
Salient feature:
- Complete range of chemical reactor obtainable in dissimilar stipulation
- Manufacturing process can utilized with SS and MS.
- Superior quality of chemical reactor is Better efficiency, Leakage proof, Genuine steel built, Advanced Technology construction, best functionality
- Wide Range Of chemical reactor is strong structure with High performance
- Customized Solutions available as per the Customer Oriented.
- Material supply in all SS Series and Alloys as required.
- Meticulous manufacture by Skilled capable works team
- In-Process quality control as per QAP and testing as per FAT Protocol
- Supply World Wide Installations supervision
- Selection and Design of most well-organized with Agitation System for necessary process by Qualified with Reputed Chemical & Mechanical Design Engineers as per the Top R&D
- Well-organized Heat Transfer Device designs like Internal coil, Dimpled, Limpet Jacket etc.
- Satisfaction Guaranteed with Slurry Processing Agitator Design, Gassing Agitator Design, Viscous Fluid Agitator Design, Vertical & Horizontal Storage and Pressure Vessel design with Bonnet Heat Exchangers
- All kind of Heat Exchanger intend from Condenser, Evaporators , Reboilers, Tube type Double pipe to large Shell etc
Watch Video for CHEMICAL REACOTRS::
Reaction Vessel, Jacketed Reaction Vessel, Limpet Coil Reaction Vessel, Stainless Steel Reaction Vessel manufacturer and supplier India
Products
- Softgel Capsule Manufacturing Equipments
- Gelatin Cooking Mixer Manufacturer
- Gelatin Holding Tank
- Reaction Vessel
- V Cone Blender Mixer
- Condenser / Heat Exchanger
- Pressure Vessels
- Distillation Unit
- Pilot Reaction Unit
- Sigma Mixer
- Ribbon Blender
- ETO Sterilizer Machine
- Ethylene Oxide Sterilizer
- ETO Sterilizer for Hospital
- Cath lab ETo Sterilizer
- Horizontal Autoclave
- Cylindrical Autoclave
- Eto Sterilizer Exporter in India
- Reaction Vessel Exporter in India
- Ribbon Blender Mixer
- sigma mixer manufacturer
- sigma mixer manufacturer india
- Ribbon Blender